We utilize a mature quality control system to test and inspect various aspects of our valve products. From chemical element analysis to sealing performance, our quality control system ensures that all valve products meet international standards.
Standard | GB/T13927-1992 | |||
Item | Shell Test | Sealing Test | ||
Testing Temperature | 5~40℃ | 5~40℃ | ||
Test Medium | Water, kerosene, or other liquids with a viscosity not greater than that of water. | Water, kerosene, or other liquids with a viscosity not greater than that of water. | ||
Test Pressure Mpa | 1.5 times the maximum allowable working pressure at 20°C. | 1.1 times the maximum allowable working pressure at 20°C. | ||
Shortest Duration of Test | Size DN(mm) | Time (s) | Size DN(mm) | Time (s) |
≤DN50 | 30s | ≤DN50 | 15s | |
DN65~DN200 | 60s | DN65~DN200 | 30s | |
≥DN250 | 180s | DN250-DN450 | 60s | |
≥DN500 | 90s | |||
Allowed Leakage Rate | There should be no visible leakage at the pressure-bearing wall, valve body, and valve cover connection, and there should be no structural damage to the shell. | There should be no visible leakage during the shortest duration of the experiment. | ||
Other Requirements | During the test, the gas inside the valve body cavity should be completely evacuated. | Before the test, any oil stains and impurities on the sealing surface should be removed. During the test, the valve body cavity should be pressurized, and the medium used should be air. | ||
If leakage occurs, the leakage location should be marked on the valve body, and the valve with leakage should be stored in the designated area for non-conforming products. |
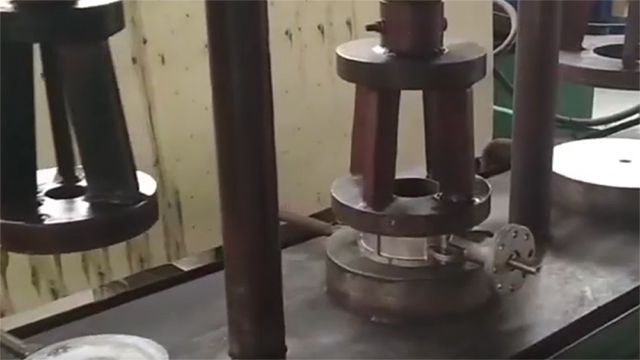
For all metal-to-metal hard-sealed valves, an air-tightness test is conducted following the requirements of GB/T26480-2011. The test is carried out at pressures ranging from 0.4 MPa to 0.7 MPa. If the leakage falls within the permissible range defined by the standard, including sealing tests for gate valves, ball valves, globe valves, upper sealing tests, and body sealing tests, the valve is considered qualified. Upper sealing tests and body tests require absolute zero leakage to ensure absolute safety in product usage.
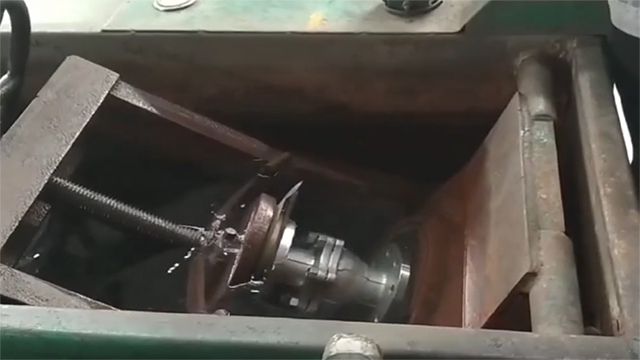
- All of our products come with an 18-month quality warranty. For soft-sealed pneumatic butterfly valves, under normal temperature conditions with water as the medium, maintaining a pipeline pressure of 1.76 MPa and an air source pressure of 0.4 MPa, they undergo 50,000 consecutive open-close cycles. Afterward, they undergo a sealing test and continue to exhibit excellent sealing performance, ensuring their reliable use.
- Our packaging includes shock-resistant bags for inner packing and wooden crates for outer packing, ensuring safe and reliable transportation without damage from impacts or compression during transit.
In addition to our internal testing processes at various stages of production, we are also open to collaborating with authorized third-party organizations to conduct additional specialized testing measures, including combustibility tests or chemical tests, to assess the reliability and durability of our valves.
Through third-party testing conducted by reputable laboratories and testing professionals, we ensure that all our industrial valves conform to various industry standards. The results provided by these organizations demonstrate the extent to which our valves meet the requirements of your business or projects.